Состояние и перспективы развития проходческих комбайнов для горных выработок
https://pgn.su/listy.html заказать прокладки из безасбестового паронита. pgn.su |
После завершения первого этапа изменений, горная промышленность России формирует финансовые ресурсы в основном путем продажи продукции. После длительного снижения производства во время реструктуризации, в последние годы наблюдается рост добычи минералов и улучшение технико-экономических показателей в горной отрасли.
Правительством страны принята «Энергетическая стратегия России на период до 2020 г.», где планируется увеличение добычи угля до 410–450 млн тонн и рост его доли в производстве электроэнергии с 34 до 44%.
Для выполнения этой стратегической задачи в указанный период потребуется обеспечить двукратный прирост производственных мощностей предприятий отрасли как за счет модернизации действующих, так и строительства новых предприятий по добыче угля и других полезных ископаемых. Рост мощностей в период до 2010 г. будет происходить за счет технического перевооружения, а в период 2011–2020 гг. – за счет коренного изменения технического уровня горного производства.
Концентрация горного производства на перспективных шахтах угольной отрасли за счет технического переоснащения очистных комплексов требует значительных изменений в ведении подготовительных работ. И в первую очередь это касается прогрессивного комбайнового способа. Уровень комбайновой проходки по ведущим угольным компаниям (УК «Кузбассуголь», УК«Кузнецкуголь») колеблется от 72 до 98 % на конец 2003 г.
Парк проходческих комбайнов в угольной отрасли составляет около 360 штук (порядка 240 из них находятся в Кузбассе). Основой этого парка являются комбайны типа ГПКС производства Копейского машиностроительного завода (по Кузбассу, например, 97%). Анализ состояния проходческих комбайнов указывает на неуклонное снижение парка новых машин. Износ комбайнов по основным угольным компаниям является настораживающим фактором в возможностях обеспечения необходимого объема подготовительных работ в угольных компаниях.
Сейчас в России, вместо ранее выпускавшихся заводами СССР для нужд угольной промышленности, других горно-добывающих отраслей и подземного строительства шести моделей комбайнов весом от 12 до 80 т, на потоке единственный массовый комбайн 1ГПКС (масса 24 т) (рис. 1) и ставится на промышленное производство базовая модель комбайна среднего класса КП-25 (масса 52 т) (рис. 2) и комбайн КП-21.
В то же время подготовленные к производству четыре типа новых современных комбайнов – КП-15 (масса 15 т), КП-20Б (масса 28 т), КП-25Н для проходки уклонов и модели с оборудованием для механизации анкерования – КП-25А (масса 58 т), а также проходческо-добычной комбайн ПДКА по типу комбайна фирмы «Джой» (масса 65 т) – не освоены производством из-за отсутствия господдержки по финансированию. Машиностроительный завод по выпуску комбайнов среднего класса (масса 40 т) и тяжелых проходческих комбайнов типа 4ПП-2М и 4ПП-5 (масса 45–80 т) остался на Украине, где было организовано производство новых проходческих комбайнов
П-110, П-220, КСП-32. Отсутствие отечественных проходческих комбайнов во всем диапазоне мощности и массы (от 8–10 до 80–100 т.) было восполнено импортом комбайнов западных зарубежных фирм и производства машиностроительных заводов Украины.
Однако в период с 1990 по 2004 г. ни один из импортных комбайнов не окупился в эксплуатации. Темпы их работы не превышают темпы проходки отечественными комбайнами, стоимость производства которых значительно ниже стоимости комбайнов зарубежных.
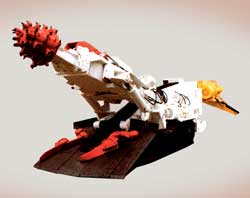
Рис. 1. Комбайн проходческий 1ГПКС
Для возрождения производства отечественных проходческих комбайнов необходимо практически заново восстановить систему организации научных и конструкторских работ по созданию проходческой техники с учетом огромного отечественного и зарубежного опыта в этом направлении, сосредоточить изготовление новых машин на предприятиях с высокоэффективной технологией, углубить подготовку инженерных и научных кадров с учетом требований рыночной экономики.
Представляется целесообразным сосредоточить деятельность по созданию проходческих комплексов на базе отечественных комбайнов, прежде всего циклического (избирательного) действия, обеспечивающих повышение темпов проходки в 3–4 раза при доведении коэффициента надежности конструкции до 0,9 и соблюдении требований безопасности горных работ.
Кроме того, необходимо сосредоточить научные исследования на создании исполнительных органов проходческих комбайнов для разрушения крепких пород, для чего использовать последние достижения в области гидроструйной технологии, вибрационной техники и других физических процессов.
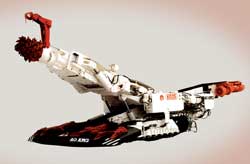
Рис. 2. Комбайн проходческий КП25
Для успешной реализации поставленных задач по созданию новой техники в условиях рыночной экономики необходимы новые подходы к организации работ, заключающиеся в организации гибких специализированных объединений. Одним из первых полностью оправдавшим возлагавшиеся на него надежды примером плодотворного взаимодействия науки и производства стал созданный еще в начале 80-х гг. учебно-научно-производственный комплекс «Тульский государственный университет (ТулГУ) – ЦНИИподземмаш – Скуратовский экспериментальный завод», задачей которого была концентрация усилий ведущих специалистов на решении актуальных задач по созданию проходческой техники, подготовка инженерных и научных кадров. В период функционирования комплекса были разработаны САПР стреловидных и планетарных исполнительных органов проходческих комбайнов, организованы оригинальная лабораторно-экспериментальная база по резанию крепких пород, аспирантура и профильные группы студентов, специализирующихся в научных и производственных подразделениях комплекса.
В этот период посредством САПР были обоснованы рациональные параметры унифицированных поперечно-осевых барабанов и продольно-осевых коронок, которые затем испытывались на шахтах Кузбасса, Воркуты и использовались в комбайнах 1ГПКС, КП-20Б, КП-25 (табл. 1). Кроме того, выполнены работы по созданию универсальных исполнительных органов стреловидного типа для проведения выработок по углю и смешанному забою применительно к комбайнам ПК-9, ЧПП-2М, а также разработана и испытана в шахтных условиях оригинальная конструкция режущей коронки с встроенным вибрационным устройством.
Таблица 1
|
На базе комбайнов КП-20Б, КП-25 «ЦНИИподземмаш» планирует создать новые высокоэффективные проходческие машины блочно-модульного построения (КП-30; КП-70), оснащенные сменными исполнительными органами в виде продольно-осевых коронок и поперечно-осевых барабанов, средствами секторного и контактного взрывозащитного орошения, навесным оборудованием для механизации работ по бурению шпуров под анкерную крепь и ее установке.
Для расширения области применения этих комбайнов планируется создать комплекты проходческого оборудования, включающие перегружатель, комплекс проветривания и обеспыливания, самоходный вагон, бурильное оборудование различных модификаций для установки анкерной крепи.
Такой комплект оборудования должен быть основой серийного изготовления проходческого комплекса с комбинированными (гусеничным и распорно-шагающим) механизмом перемещения типа КНК-6, совмещающего основные операции проведения выработок (отбойка, погрузка, крепление), и проходческих агрегатов, обеспечивающих малооперационную, высокопроизводительную поточную технологию проведения выработок при наиболее полном совмещении как основных, так и вспомогательных операций.
Шахтными испытаниями двух экспериментальных образцов сменного виброактивного органа на серийном комбайне 1ГПКС установлено, что сочетание механического резания с наложением вибрации определенной частоты и амплитуды позволит применять стреловидные комбайны с таким комбинированным органом для разрушения пород прочностью на сжатие до 100 МПа.
Результаты работы по виброактивному исполнительному органу использовали специалисты Сианьского горного института (Китай), которые совместно с ТулГУ разработали и на Нанкинском машзаводе изготовили коронку виброактивного действия для стреловидных комбайнов ELMB-75C и EBj-132B (см. табл. 1). Во время испытаний комбайна ELMB-75C на одной из шахт Китая за три месяца было пройдено 1500 м выработки в сложных горно-геологических условиях. На основании этих испытаний спроектирован комбайн EBJ-132B, промышленное производство которого осваивается в настоящее время.
Проводимые в последнее время в России и за рубежом научные исследования, направленные на изыскание новых способов и средств разрушения горных пород, показывают, что повышение производительности проходческих комбайнов без увеличения их габаритов и массы и расширение области их применения на более крепкие породы может быть достигнуто на основе гидромеханического способа разрушения, заключающегося в комбинированном воздействии на породный массив высокоскоростных струй воды и механического инструмента.
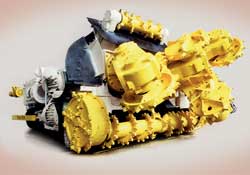
Рис. 3. Проходческо-очистной комбайн «Урал-10А»
В настоящее время ведутся разработки гидромеханических исполнительных органов со встроенным в режущую коронку преобразователем давления мультипликаторного типа и автономным источником воды высокого давления (преобразователем давления с приводным насосным блоком или насосом высокого давления), размещенным на раме комбайна или в выработке. При этом оба исполнительных органа имеют зонную подачу высоконапорной воды к режущему инструменту в зависимости от того, какая часть его контактирует с забоем. Если в исполнительном органе со встроенным в режущую коронку преобразователем давления зонная подача воды осуществляется на участке гидросистемы с низким давлением рабочей жидкости (до 25 МПа), то на исполнительном органе с автономным источником воды высокого давления используется специальное устройство управления зонным распределением воды высокого давления, состоящее из гидроуправляемых клапанов.
Гидромеханический исполнительный орган представляет собой одноступенчатый редуктор, фланец которого предусматривает возможность установки исполнительного органа через специальную проставку на стрелу комбайна. На выходном валу редуктора закрепляется промежуточный корпус с установленными в его расточках гидромультипликаторами. Гидромультипликаторы посредством каналов в выходном валу соединяются через цапфовый распределитель с гидросъемником соответственно с приводной насосной станцией и водяной магистралью. На промежуточном корпусе закрепляется коронка с гидромеханическими резцами, которые посредством коллекторов высокого давления соединяются с рабочими полостями высокого давления гидромультипликаторов.
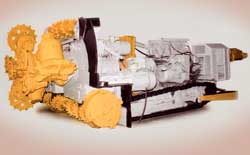
Рис. 4. Проходческо-очистной комбайн «Урал-20А»
Принцип работы такого исполнительного органа состоит в следующем. При вращении вала с гидромультипликаторами их рабочие полости низкого давления посредством цапфового распределителя на одной половине оборота соединяются с напорной, а на другой – со сливной магистралями приводной насосной станции. При соединении с напорной магистралью каждый гидромультипликатор совершает рабочий ход, а при соединении со сливной – происходит взвод гидромультипликатора под воздействием рабочей жидкости от гидросистемы взвода.
В гидромеханических исполнительных органах с автономным источником воды высокого давления устройство управления зонным распределением воды можно располагать как в стреле исполнительного органа или внутри режущей коронки, так и на раме комбайна. Подача высоконапорной воды от источника к коронке осуществляется с помощью гидросъемника и многоканального трубопровода, проходящего внутри пустотелого вала привода вращения коронки.
Эффективность гидромеханического разрушения во многом зависит от давления и расхода высокоскоростной струи воды. Эти параметры, в свою очередь, определяются гидравлической мощностью преобразователя давления. В табл. 2 представлены разработанные совместно с фирмой «НИТЕП» типоразмерный и параметрический ряды источников воды высокого давления, которые применяются в гидромеханических исполнительных органах.
Таблица 2
|
Параметрический ряд образован из десяти исполнений преобразователя давления (по признаку кратности преобразуемого низкого давления масла в высокое давление воды), а типоразмерный – из семи типов приводных насосных станций (в зависимости от мощности привода).
Из табл. 2 видно, что мощность привода источника воды высокого давления изменяется в зависимости от типоразмера в широком диапазоне – от 17 до 220 кВт (при рабочем давлении масла в гидросистеме низкого давления 25 МПа) и сопровождается увеличением расхода высоконапорной воды. При этом давление высоконапорной воды в зависимости от исполнения преобразователя давления изменяется от 65 (2-е исполнение) до 400 МПа (10-е исполнение) с одновременным уменьшением расхода воды (1-е исполнение преобразователя давления предназначено для высоконапорного орошения).
На сегодняшний день совместно с фирмой «НИТЕП» и ННЦ «ГП-ИГД им. А.А. Скочинского» разработаны, изготовлены и испытаны экспериментальные и опытные образцы таких исполнительных органов. Режущие коронки, оснащенные высокоскоростными струями воды, с использованием преобразователей давления с мощностью привода насосного блока 35–220 кВт (см. табл. 2) для комбайнов 1ГПКС (см. рис. 1) и КП-25 (см. рис. 2) обеспечивают повышение производительности по отбойке в зависимости от схемы расположения струи воды относительно резца в 2,4–3,8 и 1,8–3,4 раза соответственно по сравнению с механическим способом. Уже при использовании только струй воды давлением 150–200 МПа области применения комбайнов 1ГПКС и КП-25 расширяются на породные и смешанные забои с пределом прочности на сжатие 80–90 МПа (в этом случае комбайн 1ГПКС может заменить более тяжелый и дорогостоящий комбайн КП-25) и 100–110 МПа соответственно с производительностью не меньшей, чем при механическом разрушении.
Вторым направлением разработки проходческих комплексов и агрегатов для горной промышленности является модернизация проходческо-добычных комбайнов типа «Урал» непрерывного действия с планетарными исполнительными органами. Комплексы «Урал-10А» и «Урал-20А» (рис. 3 и 4), каждый из которых состоит из комбайна, буровой установки для анкерной крепи, бункера-перегружателя и самоходных вагонов, широко применяются в настоящее время для проведения выработок арочной формы сечением 7,8–20,2 м2 на калийных рудниках России, Белоруссии, а также при добыче пищевой соли на Украине.
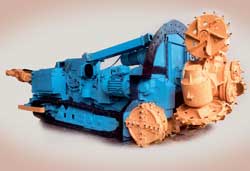
Рис. 5. Проходческо-очистной комбайн «Урал-61»
С момента начала промышленного освоения (1976 г.) эти комплексы постоянно совершенствуются за счет дальнейшей унификации, повышения надежности и долговечности работы основных узлов, автоматизации производственных процессов и улучшения условий труда обслуживающего персонала. Для этого комбайны снабжены противовибрационными закрытыми от пыли кабинами машинистов, авторегулятором нагрузки электропривода типа «ПРИЗ», аппаратурой дистанционного управления при заездах в камеру типа «АДУ», лазерной установкой с пассивным экраном для контроля за положением комбайна в забое, устройством защиты электродвигателей от перегрузки типа «КОРД»; аппаратурой, обеспечивающей полуавтоматический режим работы всего соледобывающего комплекса (комбайн, бункер-перегружатель, самоходный вагон).
Принятые в комплексах конструктивные решения на основе унификации различных типоразмеров машин, составляющей в настоящее время около 50%, являются важным преимуществом и полностью соответствуют современным требованиям конкурентоспособности машиностроительной продукции. Это подтверждается фактом стабильной их потребности в период общего спада производства: выпуск комбайнов типа «Урал-20» в 1990, 1998,1999 гг. составлял соответственно 17, 14 и 15 машин.
Заложенный в этих комплексах принцип унификации позволил предприятиям ОАО «Копейский машиностроительный завод», «КУРС», «Белгорхимпром» (Беларусь) с участием ТулГУ в последние годы развить целое направление по созданию новых машин:
- «Урал-61» (рис. 5) – комбайн, предназначенный заменить комбайн ПК-8МА (Украина) для проходки подготовительных выработок арочной формы;
- «Урал-50» (рис. 6) машина для нарезки компенсационных щелей в кровле выработки;
- «Урал-60» – для обработки почвы горизонтальных и наклонных (до ±12 ) выработок;
- «Урал-70» со стреловидным исполнительным органом для выполнения вспомогательных работ;
- МП-20 – машина погрузочная для выгрузки руды из подземных складов калийных рудников на транспортный конвейер.
В настоящее время АО «Копейский машиностроительный завод» освоил промышленный выпуск комбайна нового поколения «Урал-20Р», существенным отличием которого является замена (с целью унификации и улучшения сортности продуктов разрушения) плоско-планетарного забурника на аналогичный основному сферически-планетарный режущий орган.
Наличие такой проверенной длительным опытом эксплуатации отечественной горной техники дает основание использовать комплексы типа «Урал» для камерно-столбовой системы разработки угольных пластов и проведения в них подготовительных выработок.
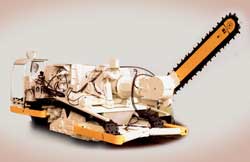
Рис. 6. Машина «Урал-50» для нарезки компенсационных щелей
Актуальность целесообразности использования комплексов типа «Урал» в угольной промышленности выражается еще и тем, что в настоящее время в Кузбассе используются проходческо-выемочные агрегаты фирмы «Джой», обладающие высокой стоимостью оборудования (до 10 млн долларов, включая технологическое сопровождение специалистами). Сопоставление технических характеристик лучших зарубежных образцов с комплексами «Урал» и расчеты показывают, что по основным параметрам они не уступают известным машинам типа «Джой», «АВМ», «Эймко» (табл. 3). При работе по камерно-столбовым и многоштрековым схемам в наиболее сложных условиях разработки пласта мощностью 3 м и сечением 15 м2 конечные результаты использования комплексов «Урал» составляют: скорость проходки 30 м/сутки (600 м/месяц), производительность по добыче 1000 т/сут. (до 20 тыс. т/месяц, или не менее 200 тыс. т в год).
Таблица 3
|
Возможная суточная нагрузка на забой соизмерима с соответствующими показателями, достигаемыми на перспективных угольных шахтах России на один очистной забой, а достигаемая скорость проходки подготовительных выработок, естественно, значительно превышает производительность стреловидных проходческих комбайнов.
Важно отметить, что применение комбайнов типа «Урал» на угольных шахтах повысит рентабельность не только горного производства, но и отечественного горного машиностроения.
Принятые направления научной деятельности учебно-научно-производственного объединения при ТулГУ получили поддержку отечественной и зарубежной научной общественности, выполнен ряд работ по конкурсным грантам, создан молодой творческий коллектив, который взял на себя всю тяжесть перестройки. При кафедре горных технологий и механизации горных работ ТулГУ создана проектно-конструкторская фирма «НИТЕП», которая укомплектована выпускниками объединения, руководство Скуратовским экспериментальным заводом взял на себя также воспитанник коллектива, организована научная магистратура.
С учетом требований производства и возможностей объединения предусматривается создание унифицированных проходческих комплексов на основе разработанных комбинированных стреловидных исполнительных органов, дальнейшего совершенствования планетарных исполнительных органов, обеспечивающих повышение сортности угледобычи за счет применения нового способа разрушения массива, оборудования и инструмента для гидромеханической и гидроабразивной технологии разрушения крепких горных пород.
Выводы:
Создание проходческих комбайнов и комплексов на уровне мировых стандартов для проведения выработок в различных горно-геологических условиях является одной из главных проблем обеспечения рентабельности шахтного производства и безопасности трудящихся в условиях рыночной экономики.
Базой организационной структуры для ускоренного создания унифицированных комбайновых комплексов должны быть научно-производственно-учебные объединения.
Для расширения области применения проходческих комбайнов избирательного действия на более крепкие породы и повышения производительности без увеличения их габаритов и массы необходимо использовать комбинированные виброактивные и гидромеханические исполнительные органы, а также оснащать эти машины современными средствами автоматизации, транспорта и крепи.
Для камерно-столбовой системы разработок полезных ископаемых следует сосредоточить работы по созданию комплектов на основе комбайнов типа «Урал» непрерывного действия с планетарными исполнительными органами, самоходных вагонов и средств возведения анкерной крепи.