Состав и функциональные возможности систем диспетчеризации гтк
Аренда яхты петербург прогулки под парусами спб яхта. minorlux.ru | https://www.leadtheway.ru сео продвижение сайта. Как сделать seo продвижение. www.leadtheway.ru |
Система диспетчеризации в горно-транспортном комплексе (ГТК) служит для автоматизированного управления работой в горной отрасли. Управляемыми объектами являются мобильные единицы в ГТК: буровые установки, самосвалы, экскаваторы, паровозы, думперы и т.д. Цель - эффективное использование рабочего времени и максимальной производительности машин и механизмов.
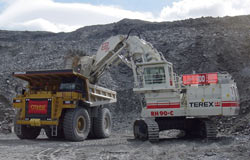
Назначение
АСУ ГТК способно обеспечить эффективное решение прикладных задач, связанных не только непосредственно с диспетчерским управлением, но и инженерным надзором, а именно:
- Управление объемом и качеством добычи полезных ископаемых, производством вскрышных работ.
- Контроль (мониторинг) выполнения технологических операций и норм эксплуатации машин и механизмов.
- Контроль выполнения проектов и планов горных и буровзрывных работ.
- Управление буровзрывными работами.
- Организация планомерного ремонта и обслуживания горно-транспортным оборудованием и автомобильными дорогами.
В результате внедрения АСУ ГТК появляется возможность более эффективно решать задачи оперативного управления работой карьера, в том числе задачи оптимизации грузопотоков, поддержания требуемого содержания полезных компонентов в руде на складах, а также управление заправками. Кроме того, появляется возможность объективной оценки деятельности служб и участков предприятия, что положительно влияет на трудовую и технологическую дисциплину персонала.
![]() |
Структура и состав
Системы управления ГТК можно разделить на три типа:
- Системы с «ручным режимом»
Это системы, предоставляющие всю необходимую информацию о технологических параметрах производимых работ и, возможно, о техническом состоянии объектов, на основе которой решение принимает диспетчер или соответствующий персонал.
- Системы с «режимом советчика»
Не только снимают информацию с датчиков, но и обрабатывают ее для выдачи диспетчеру одного оптимального или нескольких вариантов решения на выбор.
- Системы с «диалоговым режимом»
Имеют те же возможности, что и системы с «режимом советчика», но работают исходя из принципов заранее заданных критериев (условий), которые диспетчер может изменять в режиме реального времени в зависимости от обстановки.
Последнее поколение АСУ ГТК, как правило, содержит средства оптимизации процессов, которые имеют, кроме «режима советчика», полностью автоматический режим, допускаемый для тех или иных операций на основе заданных критериев оптимизации и весовых коэффициентов этих критериев. В этом режиме диспетчер только отслеживает результаты принятых системой решений, только при необходимости вмешиваясь в управление.
ДЛЯ СПРАВКИ
Назначение системы
- управление выемочно-погрузочным оборудованием и автомобильным транспортом;
- контроль и управление объемом и качеством руды;
- мониторинг управления эксплуатацией оборудования;
- управление буровыми работами.
Цели системы
- повышение эффективности использования оборудования горно-транспортного комплекса и увеличение его производительности;
- обеспечение экономии ресурсов при достижении необходимых объемов производства;
- стабилизация показателей качества руды, поступающей в переработку;
- снижение расхода топлива, шин, оптимизация загрузки транспортных средств;
- организация планомерного ремонта и обслуживания транспортного оборудования;
- повышение трудовой и технологической дисциплины.
Функции системы
- автоматический сбор информации в режиме реального времени;
- управление оборудованием в режиме реального времени;
- автоматическое диспетчерирование;
- управление качеством руды с учетом функционирования рудоконтрольных станций и усреднительных складов при различных требованиях к формированию рудопотоков;
- оперативный контроль движения руды, вскрыши и в целом горной массы;
- ведение карты карьера в реальном времени;
- контроль соблюдения маршрутов движения и пунктов разгрузки;
- контроль скорости движения автосамосвалов;
- менеджеринг исключительных ситуаций;
- мониторинг работы двигателей автосамосвалов;
- мониторинг заправок и расхода топлива автосамосвалами;
- контроль возможного хищения топлива;
- контроль загрузки автосамосвалов;
- мониторинг эксплуатации шин;
- мониторинг времени технического обслуживания оборудования;
- ведение базы данных Oracle и системы отчетности.
История внедрения систем диспетчеризации ГТК в горно-добывающей промышленности России. Отечественные системы диспетчеризации на открытых горных работах
Развитие АСУ ТП, особенно на технологическом транспорте, происходило на протяжении последних 40–45 лет. Известны такие системы, как «Карат», «Пуск», «Томусинский», «Кварцит» и «Гранит», которые работают в «режиме советчика» по замкнутому циклу.
Система «Карат» разработана Центральным научно-исследовательским институтом комплексной автоматизации (ЦНИИКА) и предназначена для решения следующих задач горного производства:
- оперативного планирования объемов добычи руды экскаваторами в режиме усреднения ее качества;
- оптимального планирования транспортных средств и распределения их по пунктам погрузки и разгрузки;
- сбора первичной информации, ее обработки и выдачи результатов расчета оперативных показателей работы экскаваторно-автомобильного
- комплекса для анализа, выработки решений и планирования работы на следующие смены.
Система осуществляет ряд функций по управлению и контролю технологических процессов в карьере:
- распределение потока технологического транспорта по пунктам погрузки для выполнения сменного плана горных работ и обеспечения требуемого содержания полезного продукта в рудах, поставляемых на обогатительную фабрику;
- выбор пункта погрузки и маршрута следования каждого автосамосвала с целью уменьшения суммарных простоев погрузочного и транспортного оборудования;
- учет работы экскаваторов и автосамосвалов;
- учет объемов горной массы по пунктам разгрузки и со всего карьера в целом.
Она позволяет опознавать номера автосамосвалов на контрольных пунктах, взвешивать их по ходу, информировать о перевозимом объеме горной массы водителей автосамосвалов и оператора, контролировать автосамосвал при сходе его с линии. При резких изменениях производственной ситуации (например, выход из строя погрузочных экскаваторов, перегрузочных пунктов, обогатительных фабрик, изменение содержания руды в забоях и т.д.) производится перезакрепление автосамосвалов. (В системе «Искра» указанные процессы осуществляются автоматически с помощью ЭВМ, без вмешательства диспетчера).
Система «Карат» была внедрена на карьере «Мир».
Основная функция модернизированной системы «Карат-М» состоит в оперативном управлении изменением потока транспортных единиц. В результате диспетчер получает возможность непосредственно воздействовать не только на отдельные автосамосвалы, но через них на экскаваторы, а тем самым – на качественные и количественные параметры исходящего потока руды, на скорость подвигания добычных и вскрышных забоев.
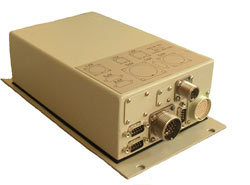
Программируемый бортовой контроллер СКЗ (системы контроля загрузки) системы диспетчеризации «КАРЬЕР».
Таким образом, в отличие от системы «Карат», система «Карат-М» работает в так называемом «диалоговом режиме», причем информация о состоянии экскаваторов, а также положении на пунктах разгрузки передается машинистами и операторами непосредственно на пункт управления диспетчеру по радио или телефонной связи.
Внедрение этой системы позволило снизить простои автотранспорта в ожидании погрузки в среднем на 15–20%, простои экскаватора в ожидании транспорта – на 20%, повысить однородность качества руды, поступающей на обогатительную фабрику, увеличить коэффициент использования грузоподъемности автотранспорта на 17%, повысить культуру производства.
В то же время «Карат-М» и аналогичные ей системы не позволяли осуществлять контроль за многими важными эксплуатационными характеристиками работы автосамосвалов, что приводило к завышенным затратам на горюче-смазочные материалы, автомобильные шины, ремонты и техническое обслуживание. В настоящее время из-за устаревшей элементной базы системы подобного типа не используются.
Система «Кварцит», внедренная на Ингулецком ГОКе (Украина), функционирует в «ручном режиме». Наряду с функциями учета работы экскаваторов и автосамосвалов она позволяет производить ручное адресование автосамосвалов на погрузку и разгрузку в соответствии с планом-графиком, рассчитанным в информационном вычислительном центре.
В ее состав входят автомобильные весы, датчик номера автосамосвала, устройство опознавания и диспетчерский пульт. На запоминающий регистр диспетчерского пульта информация о количестве горной массы поступает с автомобильных весов, о номере автосамосвала – с устройства опознавания, о номере погрузочного экскаватора и о месте разгрузки – с наборного поля диспетчерского пульта. Сформированная информация выводится на перфоленту и на световое табло автомобильных весов. При въезде автосамосвала в карьер на световом табло высвечивается адрес погрузки и разгрузки, набираемый вручную диспетчером на наборном поле пульта.
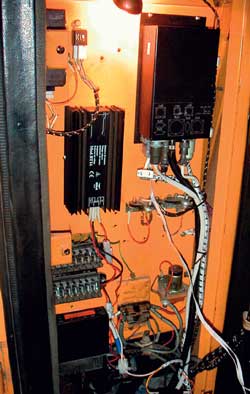
Системой «КАРЬЕР» предусматривается несколько вариантов бортового оснащения экскаваторов:
- базовый вариант, не предусматривающий высокоточного позиционирования;
- вариант с высокоточным позиционированием ковша экскаватора с учетом дирекционного угла направления стрелы экскаватора;
- вариант с высокоточным позиционированием при помощи одной GPS антенны без определения дирекционного угла направления стрелы экскаватора.
Более совершенными системами, прошедшими опытно-промышленную эксплуатацию, являются «Комплекс-АТ» и «Гермес», относящиеся к классу информационно-управляющих систем, которые реализуют как информационно-вычислительные функции, так и управляющие и вычислительные.
Система «Гермес», внедренная на СевГОКе (Украина), реализует широкий спектр информационно-вычислительных функций: сбор информации о массе грузов, перевозимых автосамосвалами и погруженных экскаваторами, о состоянии экскаваторов и технических средств; подготовку информации для АСУ верхнего уровня; контроль и регистрацию отклонений от заданного режима; отображение информации.
Автоматизированная система управления погрузочно-транспортными работами «Комплекс-АТ» была внедрена на Соколовском карьере.
Анализ функциональных возможностей рассмотренных систем «Гермес» и «Комплекс-АТ» показывает, что учет технико-экономических эксплуатационных показателей осуществлялся в основном за счет сокращения времени простоев благодаря рациональному адресованию транспортных средств к погрузочному оборудованию и перегрузочным пунктам, где решается важнейшая технико-экономическая задача усреднения качественного состава руды.
Результаты использования рассмотренных систем управления автотранспортом показали, что системы «Карат» и «Пуск» целесообразно применять на карьерах производительностью 5–10 млн т сырой руды, а системы «Комплекс-АТ» и «Гермес» – свыше 10 млн т в год.
В Казахском политехническом институте была создана система диспетчеризации «Авто».
Ее функциональная структура включает в себя подсистемы планирования работы экскаваторно-автомобильным комплексом карьера на смену, оперативного управления маршрутом следования автосамосвала, учета добытой и перевезенной горной массы за смену с нарастающим итогом, контроля выполнения плановых заданий экскаваторами и автосамосвалами, контроля и учета объемов и качества руды на внутрикарьерных перегрузочных складах, формирования отчетных данных и технико-экономических показателей с представлением их оперативно-управляющему персоналу.
Планирование и управление в системе осуществляется в режиме усреднения качества руды на внутрикарьерных перегрузочных складах с минимизацией транспортной работы.
После опытной проверки работоспособности система «Авто» была внедрена на комбинате «Кустанайасбест» (Казахстан), что позволило увеличить сменную производительность парка автосамосвалов в карьере за счет сокращения простоя горно-транспортного оборудования. В то же время, контроль и учет именно эксплуатационных затрат на карьерные автосамосвалы напрямую не осуществлялся.
Одной из первых, прямо учитывающих эксплуатационные затраты на карьерные автосамосвалы, была система, введенная в эксплуатацию в 1984 г. на автопредприятии технологического автотранспорта ПО «Якутуголь», обслуживающего разрез «Нерюнгринский», разработанная институтом «Гипроуглеавтоматизация» для автопредприятий горно-добывающей промышленности с открытым способом добычи полезных ископаемых. Созданная на базе вычислительных машин серии СМ она позволяет решать следующий комплекс задач: планирование грузоперевозок, учет и анализ показателей работы автомобилей, планирование технологического обслуживания, расчет заработной платы водителей.
Однако анализ ее работы показал, что такие элементы контроля эксплуатационных затрат, как несанкционированные отклонения от заданного маршрута и слив топлива из топливного бака, а также контроль за состоянием важнейших агрегатов автосамосвала в режиме реального времени остались без внимания.
Оптимальными условиями функционирования этой системы являются следующие технические показатели: объем перевозок – до 200 млн м3; длина ездки – от 1 до 10 км; число автосамосвалов – не более 300, а экскаваторов – 40 единиц; при этом грузоподъемность автосамосвалов – от 27 до 200 т, а вместимость ковша – от 4 до 20 м3.
Универсальная автоматизированная система управления технологическими процессами на руднике открытых работ – АСУ ТП РОР – была разработана и внедрена Северокавказским филиалом Всесоюзного научно-исследовательского и конструкторского института «Цветметавтоматика» (СКФ ВНИКИЦМА) на Тырныаузском комбинате в 1986 г. Ее техническое обеспечение включает в себя устройства считывания информации с автосамосвалов индуктивного типа, кабельные и радиотехнические каналы связи, управляющую вычислительную машину СМ-2М, выдающую советы по управлению и отчетные документы.
Применительно к автотранспорту система выполняет следующие информационные задачи: оперативный учет объемов выработки каждого автосамосвала, учет объемов автооткатки в тонно-километрах, анализ работы автосамосвалов, периодический контроль за нахождением автосамосвала на линии с выдачей оператору номеров автосамосвалов, сошедших с линии, а также учет средней загрузки автосамосвалов.
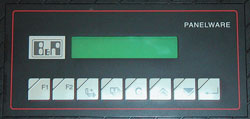
В комплектацию контроллера СКЗ исполнения 02.01 включена панель визуализации B&R Panel Ware, позволяющая обмениваться с диспетчерской службой стандартными сообщениями (имеет дисплей в 2 строки по 20 символов) (система «КАРЬЕР»).
Управляющие задачи системы состоят в оперативном распределении автосамосвалов между вскрышными и рудными экскаваторами в начале смены, коррекции сменных плановых заданий в случае незапланированных ситуаций и определении адресов погрузки и разгрузки автосамосвалов.
Оператор может перераспределять автосамосвалы между экскаваторами при возникновении сбоев технологического процесса и корректировать текущую информацию при сбоях в работе автосамосвалов.
Задача представления оператору информации о ходе работы автотранспорта позволяет получать таблицу средней загрузки автосамосвалов по типам, таблицу номеров автосамосвалов, работающих на линии, и сводку об их работе.
Основные принципы работы и структуру современных систем диспетчеризации управления карьерными автосамосвалами можно проиллюстрировать на примере отечественной системы диспетчеризации «КАРЬЕР» разработки ООО «ВИСТ Групп».
АСУ ГТК «КАРЬЕР» разработана с целью повышения качества оперативного управления работой большегрузных автосамосвалов. Это достигается благодаря непрерывному обеспечению диспетчерского и управленческого персонала полной информацией о текущем положении и техническом состоянии находящихся в рабочей зоне самосвалов (для этого последние оснащены бортовыми комплектами оборудования): количество сделанных рейсов, масса перевезенных грузов, расход топлива и другие характеристики работы транспортных средств.
Для определения в реальном времени положения (а значит, направления движения, скорости и вида работы) мобильного объекта в системе «КАРЬЕР» используется спутниковое определение координат с применением приемников глобальной системы позиционирования GPS.
Система «КАРЬЕР» обеспечивает:
- надежную, непрерывную работу диспетчерского и инженерно-технического персонала, осуществляющего автоматизированный мониторинг в режиме реального времени местоположения, выполнения операций и сменных заданий мобильными объектами, занятыми на производстве;
- централизацию и оперативность управления работой большегрузных автосамосвалов и других мобильных объектов, автоматизированную оптимизацию маршрутов в зависимости от заданий и изменяющейся обстановки;
- ведение статистической информации и обеспечение оперативной отчетности с предоставлением пользователям инструментария для генерации собственных отчетов;
- доступ пользователей только к тем данным, которые необходимы им для выполнения своих служебных обязанностей;
- возможность сохранения и при необходимости восстановления всех введенных в систему данных, в том числе и при аварийном отключении питания.
Внедрение системы позволяет повысить эффективность использования техники: резко сокращаются простои, как самосвалов, так и экскаваторов, фактически исключаются недогрузы и перегрузы, за счет оптимизации скоростного режима уменьшается износ двигателей, шин и других узлов.
АСУ «КАРЬЕР» использует широко известные, популярные продукты и технологии – такие, как Oracle, Map Objects, Crystal Reports и другие.
Принципы построения системы позволяют расширять ее функциональность, добавляя новые модули, алгоритмы обработки, формы ввода и отчеты без перекомпиляции уже работающих модулей.
Программное обеспечение системы позволяет создавать множество рабочих мест пользователей, назначая им определенные права по использованию данных (разграничение доступа). Архивирование информации производится автоматически или по команде администратора.
Программно-аппаратный комплекс системы диспетчеризации состоит из:
- диспетчерского центра (ДЦ), включающего радиооборудование, серверы и программное обеспечение;
- бортового оборудования, устанавливаемого на транспортные средства.
ДЦ системы состоит из радионавигационного (РНК) и информационно-вычислительного (ИВК) комплексов. Предусматриваются технические исполнения с размещением обоих комплексов в одном и в разных корпусах (стойках), позволяющие применять территориальное разнесение комплексов со связью по оптоволоконным каналам ЛВС. В первом случае весь ДЦ устанавливается на борту карьера, в условиях наилучшей радиовидимости мобильных объектов, включенных в систему. Во втором, на борту, например, в пункте горного диспетчера, устанавливается только радионавигационная часть ДЦ, а стойка информационно-вычислительного комплекса, содержащая рабочую базу данных и программное обеспечение системы, располагается в «серверной», т.е. в условиях, наиболее благоприятных для обслуживания специалистами подразделения АСУ. Но при этом абсолютно необходимым условием является связь между серверами этих двух комплексов по высокоскоростному оптоволоконному каналу. Если сегменты ЛВС (корпоративной сети) предприятия построены с использованием современных высокоскоростных технологий передачи данных и соответствующей сетевой аппаратуры, то двухсторонняя связь РНК и ИВК может быть осуществлена через корпоративную сеть (ЛВС) предприятия.
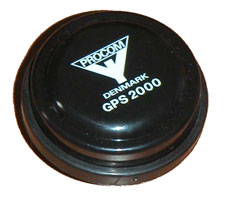
GPS антенна.
Данные о местоположении и состоянии машины собираются и накапливаются в ее бортовом контроллере. На основе этой информации он определяет первичные события, происходящие с мобильным объектом (для самосвала это погрузка, разгрузка, заправка, остановка и т.д.). Информация о событиях вместе с оперативной информацией автоматически передается в ДЦ (непосредственно принимается радионавигационным комплексом и передается в информационно-вычислительный комплекс). Обмен данными между ДЦ и мобильными объектами осуществляется с помощью радиосвязи на УКВ частотах 400–470 МГц, но может быть организован на основе систем связи TETRA, MESH и др.
В ДЦ информация бортовых контроллеров обрабатывается, архивируется и визуализируется на экранах диспетчера и др. специалистов в виде условных значков, наложенных на актуальный план горных работ предприятия. Данные бортовых контроллеров дополняются новой информацией (например, для рейса самосвала определяются экскаватор, пункт разгрузки, вид груза и другие характеристики), а также фиксируются вторичные события (например, длительный простой без уважительной причины). В результате обработки и анализа накопленных данных производится автоматическое составление отчетных документов о работе предприятия, его участков, отдельных машин, персонала.
Из ДЦ на транспортные средства передаются текстовые сообщения от диспетчера (появляются на индикаторной панели в кабине водителя) и служебные данные.
Типичный для автоматизированной системы диспетчеризации «КАРЬЕР» состав бортового оборудования состоит из следующих компонентов:
- Программируемый бортовой контроллер СКЗ (система контроля загрузки). Выполняется в нескольких исполнениях. В комплектацию контроллера СКЗ исполнения 02.01 включена панель визуализации B&R Panel Ware, позволяющая обмениваться с диспетчерской службой стандартными сообщениями (имеет дисплей в 2 строки по 20 символов);
- GPS приемник и GPS антенна.
- УКВ радиостанция с УКВ антенной (как и все компоненты оборудования, радиостанция должна находиться в закрытом отсеке).
- Комплект датчиков (опционно: датчики веса, уровня топлива, инклинометр и т.д. в зависимости от типа объекта).
Бортовой контроллер периодически опрашивает датчики давления в подвесках самосвала, датчик уровня топлива и инклинометр, обрабатывает сигналы «подъем платформы», «ход вперед», «ход назад», «сборка схемы», сигнал с датчика вращения колеса и информацию с GPS приемника. Кроме этого, контроллер принимает и обрабатывает информацию, поступающую по радиоканалу с диспетчерского центра, и обрабатывает информацию, вводимую водителем на функциональной клавиатуре панели, установленной в кабине.
На панели визуализации водитель в любое время может увидеть и проконтролировать:
- вес груза;
- количество рейсов с начала смены;
- скорость движения;
- пробег груженого и порожнего самосвала за последний рейс;
- информацию об исправности системы;
- текстовое сообщение, посланное диспетчером или автоматически;
- и т.д.
Вес груза определяется с точностью до 5% от максимальной загрузки самосвала. Ошибка взвешивания носит несистематический характер, поэтому фактически средняя ошибка взвешивания груза за всю смену не превышает 1–2% от максимальной загрузки самосвала.
В системе применяется наружная световая индикация степени загрузки автосамосвала, и машинист экскаватора может учитывать степень загрузки по сигнальным фонарям самосвала для избежания перегруза. Кроме того, имеется возможность контролировать угол наклона площадки при погрузке при помощи одной из разновидности датчиков – инклинометров, что увеличивает точность определения веса груза.
Точность определения уровня топлива в баке составляет 1–3% от объема бака в зависимости от типа датчика. Эта точность достаточна для исключения несанкционированного слива топлива и определения расхода топлива за смену. Для определения удельного расхода топлива по определенному маршруту используются усредненные данные по нескольким рейсам.
Водитель (машинист) имеет возможность как принимать на панель визуализации сообщения диспетчера, так и передавать в диспетчерский центр сообщения: начало, окончание смены, тип простоя и т.п. Список стандартных сообщений не является жестко запрограммированным, он согласовывается на этапе технического проектирования и вводится в систему во время пусконаладочных работ.
Для экскаваторов предусматривается несколько вариантов бортового оснащения:
- Базовый вариант, не предусматривающий высокоточного позиционирования. В этом случае координаты ковша экскаватора во время черпания определяются с точностью до 3 метров, а большинство определений обладает точностью около 1,5 метра. Высотная отметка не определяется. Данный вариант решения подходит для большинства заказчиков.
- Вариант с высокоточным позиционированием ковша экскаватора с учетом дирекционного угла направления стрелы экскаватора. Вариант предусматривает контроль высотной отметки. Реализуется с помощью двухантенной технологии GPS.
- Вариант с высокоточным позиционированием при помощи одной GPS антенны без определения дирекционного угла направления стрелы экскаватора. По всей видимости, это оптимальный вариант оснащения, если есть потребность высокоточных определений координат только самого экскаватора. При этом есть возможность определения фактического направления отработки забоя.
Зарубежные системы диспетчеризации для открытых работ
Можно выделить порядка 10 наиболее интересных типов систем управления горно-транспортным комплексом из числа появившихся в мире за последние 20 лет.
Система, внедренная на медном карьере недалеко от г. Туссон (США).
Для фиксирования продвижения автосамосвалов применялись контрольные точки, из которых информация поступала на контрольный пункт. Туда же с экскаваторов поступала информация о начале и окончании погрузки. Применялась голосовая радиосвязь, однако адрес пункта следования передавался водителю на цифровое табло.
Особенности системы:
- «Оптимизация», заключавшаяся в решении задач линейного программирования: постановка задач изменялась в соответствии с календарным планом, погодными условиями и количеством задействованных мобильных объектов.
- Работа в диалоговом режиме: сначала вводились новые исходные данные, затем ЭВМ решала задачу оптимизации, после чего оптимальное распределение ТС передавалось водителям по радиосвязи.
Таким образом, применялся открытый цикл. Практика показала, что при этом производительность повышается на 20% и более.
Системы компании Quebec Cartier Mining (Канада).
Система имела центральный вычислительный центр, управляющий как самосвалами, движущимися по предопределенным маршрутам, так и 90 группами оборудования фабрики, а кроме того, дробильным отделением и процессами обогащения железной руды.
Одной из современных является система RAN фирмы Pincot, Allen and Holt Inc. (США).
Запоминающее устройство компьютерной системы RAN способно хранить статистические сведения, касающиеся 30 погрузочных механизмов, 30 разгрузочных пунктов, 120 автосамосвалов различной грузоподъемности, 30 автоматических заправочных станций и 5 крупных рудных складов.
Система RAN представляет непосредственную связь между компьютером и работающим горным оборудованием. В результате выдаются точные, полученные в реальном масштабе времени сведения о грузопотоках, времени движения каждого автосамосвала и т.д. Все это способствует лучшему использованию оборудования, благодаря чему на 25% возросла производительность карьера и значительно снизились капитальные и эксплуатационные расходы.
Система автоматического управления автосамосвалом (САУА) компании Unit Rig Equipment, характерная отсутствием водителя в кабине.
Система имеет в своем составе дорожное оборудование, включающее кабель с глубиною заложения 0,45 м и блоки управления. По кабелю подаются сигналы, управляющие скоростью, направлением движения, разгрузкой автосамосвалов, звуковыми сигналами и прочими параметрами. Определяется расстояние между автосамосвалами. Местонахождение каждого автосамосвала отображается на центральном табло.
Экономичность этой системы была проверена на медно-рудном карьере, где работали 10 экскаваторов и 54 автосамосвала. Время использования экскаваторов было увеличено на 7%, коэффициент использования автосамосвалов вырос на 25%.
В результате совместное использование систем САУА и диспетчеризации позволило уменьшить парк автосамосвалов и сократить эксплуатационные расходы на 25%.
Система Dispatch разработки компании Modular Mining Systems, внедренная в 1980 г. на карьере Tiron (США). Затем многократно модернизированная; действует по настоящее время.
Функционирует в реальном масштабе времени, является динамической и поэтому имеется возможность непрерывного управления автосамосвалами для выбора оптимального маршрута. Оптимизация маршрута производится согласно выбранному критерию путем применения методов линейного программирования.
Система использует спутниковую навигацию. Данные отображаются на дисплее в удобной графической форме. Есть динамические средства оценки эффективности использования автосамосвалов.
Благодаря применению системы Dispatch производительность погрузочно-транспортного комплекса повысилась в среднем на 11%. Система исключила неправильное назначение автосамосвалов за счет визуального контроля на дисплеях.
К настоящему времени разработками компании Modular Mining Systems воспользовались более 105 карьеров и 25 шахт. Ее доля на рынке систем диспетчеризации составляет порядка 90%.
Начиная с 1983 года, выпускает свою АСУ ГТК компания Wenco International Mining Systems.
Ее современная модификация использует спутниковое определение координат мобильных объектов с помощью GPS приемников, осуществляет мониторинг состояния и диспетчеризацию мобильных объектов.
Система автоматически и с высокой точностью фиксирует все составляющие погрузочно-транспортного цикла в реальном времени: «погрузка – движение в груженом состоянии – ожидание разгрузки – разгрузка – движение порожняком – ожидание погрузки».
Записываются данные о производительности, для каждой погрузки ведется учет места погрузки, номера экскаватора, номера автосамосвала, табельных номеров операторов, количества погруженной массы, качества сырья, пункта разгрузки.
Учитываются простои по различным причинам: заправка топливом, пересменка, перерыв на обед т.д.
Вся информация, касающаяся работы мобильных объектов, отображается в режиме реального времени в диспетчерском центре и офисе рудника. Руководитель и диспетчер могут вести мониторинг всех событий, происходящих в карьере, в т.ч. они могут поручить системе оптимизировать процесс производства на основе эффективного распределения автосамосвалов или самостоятельно принимать решения на основе получаемой информации.
Различные модификации системы компании Wenco были использованы и внедрены на многих горно-добывающих предприятиях. Например, на рудниках Кумтор (Киргизия) и Syncrude (Канада), на железнорудном предприятии Steel Minntac Mine (шт. Минисота, США). Система реализована на одном из карьеров АК «АЛРОСА».
Диспетчеризация железнодорожного транспорта в карьерах
Особое значение имеет диспетчеризация железнодорожного транспорта в карьерах. Железнодорожный комплекс (ЖДК) промышленного предприятия представляет сложную систему, объединяющую железные дороги, мобильные объекты (локомотивы и вагоны) и принадлежащие предприятию станции. К задачам управления ЖДК относятся: управление движением на железнодорожных станциях, контроль состояния подвижного состава и путей, отслеживание местоположения, скорости и других параметров мобильных объектов, формирование оптимальных маршрутов движения, получение и обработка другой навигационной информации.
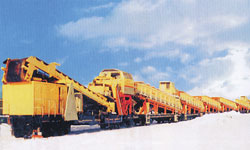
На подземных работах развитие систем диспетчеризации ГТК идет в направлении полной автоматизации погрузочно-транспортного процесса.
Развитие открытого способа разработки полезных ископаемых, как правило, сопровождается увеличением глубины карьеров и усложнением ряда других горно-технических условий, при которых значительно повышается роль карьерного транспорта. Это наиболее сложное и трудоемкое звено технологического процесса разработки месторождений полезных ископаемых, в значительной степени определяющее условия и показатели работы других структурных подразделений и предприятий в целом. При этом значительная доля из общего объема перевозок приходится на железнодорожный транспорт, являющийся наиболее надежным в различных климатических условиях. Благодаря низкой себестоимости перевозок железнодорожный транспорт при больших объемах производства и значительных расстояниях обеспечивает более высокие технико-экономические показатели эксплуатации, чем другие виды транспорта. Увеличение выпуска продукции на промышленных предприятиях сопровождается увеличением транспортных потоков как входящих, так и исходящих грузов.
Основные задачи системы диспетчеризации железнодорожного транспорта:
- информационная поддержка принятия решений при оперативном управлении погрузочно-разгрузочными работами и грузовыми перевозками на железнодорожном транспорте;
- предоставление технологическому и управленческому персоналу оперативной информации о положении подвижного состава на территории предприятия;
- ведение учета рейсов и расхода топлива;
- учет и анализ простоев вагонов;
- учет и анализ нарушений железнодорожных перевозок, а также штрафных санкций, налагаемых за эти нарушения.
Системы диспетчеризации на подземных работах
На подземных работах развитие систем диспетчеризации ГТК идет в направлении полной автоматизации погрузочно-транспортного процесса (т.е. без участия операторов, которые в данном случае являются лишь наблюдателями, контролируя правильность его протекания). Такая система внедрена, например, на подземном руднике Kiruna (Швеция). Аналогичные работы проведены в Канаде, Австрии и Финляндии на погрузочно-доставочных машинах (ПДМ).
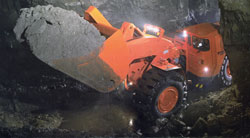
Особое значение имеет диспетчеризация железнодорожного транспорта в карьерах.
Существуют автоматизированные системы Acooptrams («вагонетка с ковшом») известные как roboscoops. Системы одного из лидеров в этой области Sandvik Tamrock испытываются на исследовательской шахте в Тампере. В одной из них навигация обеспечивается с использованием двухмерных моделей профиля стены штрека и системы точного расчета местоположения. Профиль стены сканируется двумя лазерными сканерами, один спереди и один сзади ПДМ. Такая система способна автоматизировать работу ковша при проведении операции погрузки и откатку машины.
В руднике Kiruna, как было указано выше, ПДМ управляются дистанционно, а операции откатки и разгрузки автоматизированы. Для реализации автоматизированной откатки применены отражатели, подвешенные на сторонах штрека, благодаря чему ПДМ может двигаться по заданному пути.
В Австралии продолжается разработка автономной ПДМ компанией Caterpillar Elphinstone. Этот проект интегрирует результаты выполненных на CMTE работ по автоматизированному управлению машиной с помощью лазерных сканеров, и AutoDig – автоматизированной системе загрузки ковша для фронтальных погрузчиков и ПДМ.
Компания Inco работает с несколькими ПДМ, используя удаленное управление. Откатка и разгрузка полностью автоматизированы, а погрузка осуществляется под управлением оператора, наблюдающего за процессом с помощью видеокамеры.
Однако ни в одном из рассмотренных выше проектов не используются системы стереометрического видения для зондирования и моделирования горной среды. Тогда как стереометрическое зондирование позволяет собрать большой объем информации, который может быть использован в дальнейшем. А ведь чтобы полностью автоматизировать процесс погрузки ПДМ, сначала необходимо разработать систему, «понимающую», в каких условиях работает машина. «Стереометрия» как раз позволяет понять условия и построить трехмерные связи наблюдаемых объектов. В результате вся система (включая оператора) может давать более эффективные и безопасные задания на погрузку. Подобные системы диспетчеризации разработаны и реализуются на ряде зарубежных подземных рудников для ГТК на базе локомотивной откатки (система диспетчеризации ГТК на базе оборудования рельсового транспорта компании Nordic, Канада).